Uneven powder thickness is one of the most common—and costly—issues in powder coating operations. Whether you’re seeing thin edges, overbuilt corners, or visible texture inconsistencies, this problem can lead to product rejection, coating cracks, and customer complaints. From our factory’s 20 years of experience, this issue often hides in the smallest details: electrostatics, air pressure, conveyor rhythm, or even worker habits.
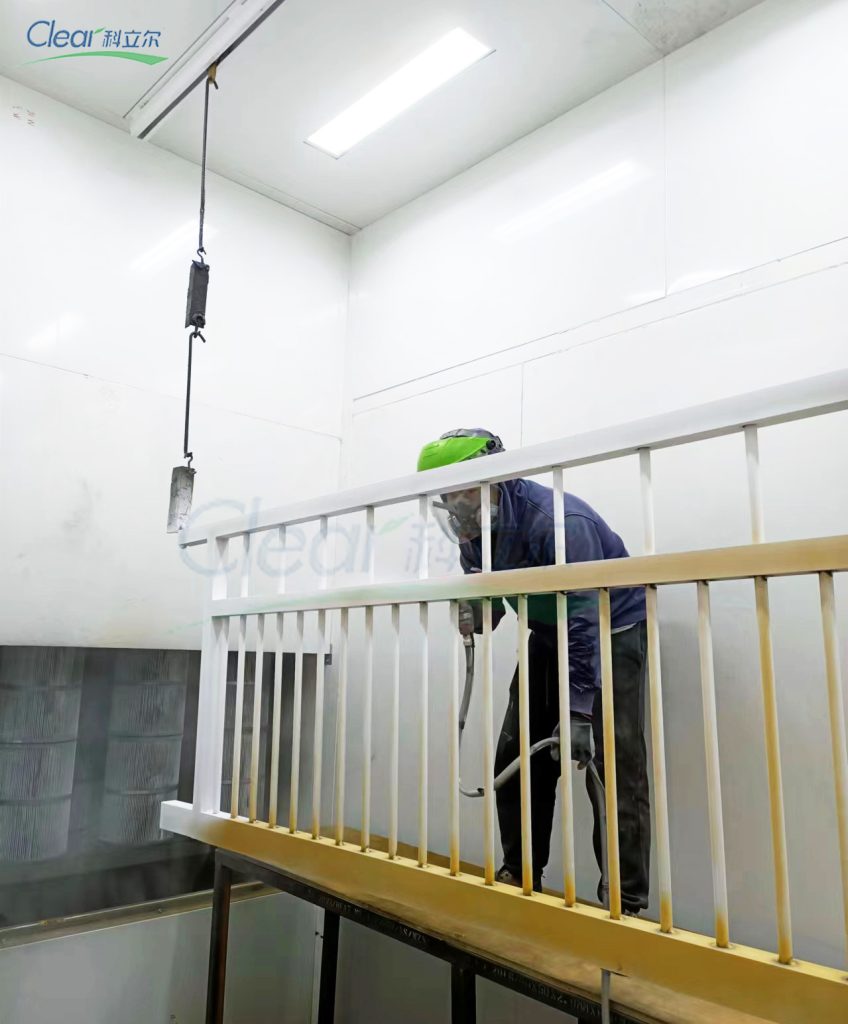
🔹 1. Common Causes of Uneven Powder Thickness
Poor grounding: Electrostatic charge cannot evenly attract powder.
Improper gun positioning: Wrong angles or distance cause over/undercoating.
Unstable air pressure: Sudden fluctuations in PSI disrupt powder cloud.
Part geometry: Sharp corners or recessed areas require special handling.
Inconsistent conveyor speed: Spray timing mismatches part flow.
🔹 2. How to Diagnose the Problem
Use a dry film thickness gauge across different part areas.
Look for areas with build-up near edges or undercoated corners.
Inspect gun calibration and powder output.
Record air supply PSI during production.
Check conveyor for jerks or hesitations.
🔹 3. Step-by-Step Fixing Process
1. Check grounding resistance of part hangers (target < 1 MΩ).
2. Reposition guns to ensure even angle and distance.
3. Stabilize compressed air with a regulator and dryer.
4. Adjust conveyor speed to better match spray zone length.
5. Add auxiliary guns or reposition parts for complex shapes.
6. Conduct test runs and re-measure thickness until consistency is achieved.
🔹 4. Pro Tips from Our Factory
Clean all spray gun nozzles every shift.
Use a rotating hanger for uneven geometries.
Avoid KV settings over 80 for thin or sharp-edged parts.
For large parts, install airflow stabilizers in the booth.
🔹 5. When to Consider Equipment Replacement
Guns show inconsistent output despite cleaning.
Conveyor vibration is causing part shaking.
Powder feeder motor doesn’t maintain steady output.
🔹 6. Conclusion
Uneven powder thickness isn’t just a quality issue—it’s a signal that your line needs attention. With the right diagnostics and adjustment, this common flaw can be eliminated entirely. Our team has helped dozens of factories optimize their coating consistency. If you need layout redesign, on-site diagnosis, or upgrade suggestions, we’re here to help.
🔹 FAQ Section
Q1: Can I still ship parts with slight powder variation?
A: Not recommended. Even minor thickness differences can affect durability and customer perception.
Q2: Will higher KV voltage improve coverage?
A: Not always. Higher voltage can actually cause back ionization or excessive build-up on corners.
Q3: Should I rotate parts during spraying?
A: Yes, especially for irregular or 3D parts. Rotating helps reach shadowed zones.